Sourav Ghosh
Operation Analyst
Classic Fashion Apparel Ltd, Jordan
Email: souravghosh090@gmail.com
Introduction:
Industry is moving toward 4.0, by matching the foot step garment industry is also moving toward 4.0. Denim washing is also not behind in this race. Denim washing is moving toward sustainability. Laser is a milestone to that path only. Making a pair of denim is labor-intensive work and takes a long time. Lasers make this process effortless. Lasers can finish a pair of jeans in 90 seconds, compared with up to 20 minutes for hand finishing.
Different parts of the Laser machine:
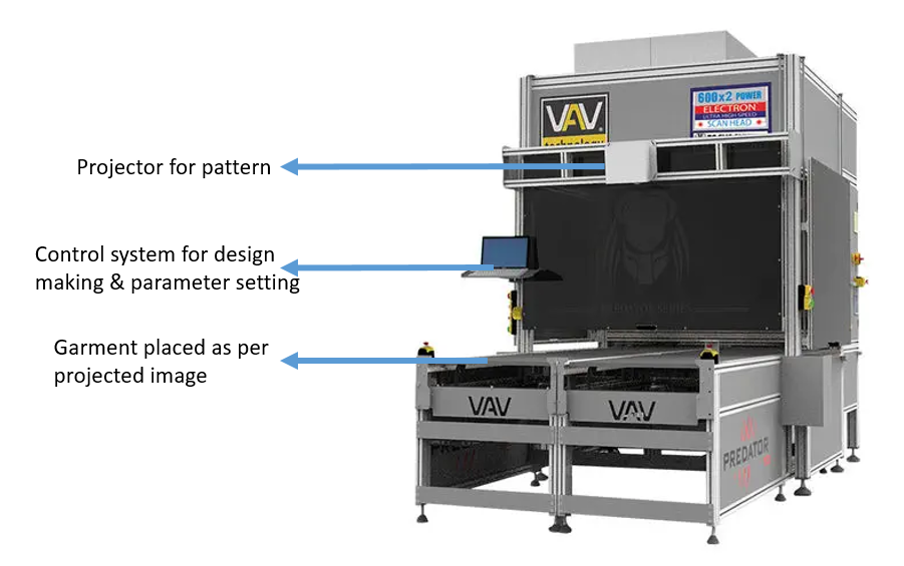
Pic: Different part of the laser machine
Process Flow of the laser department:
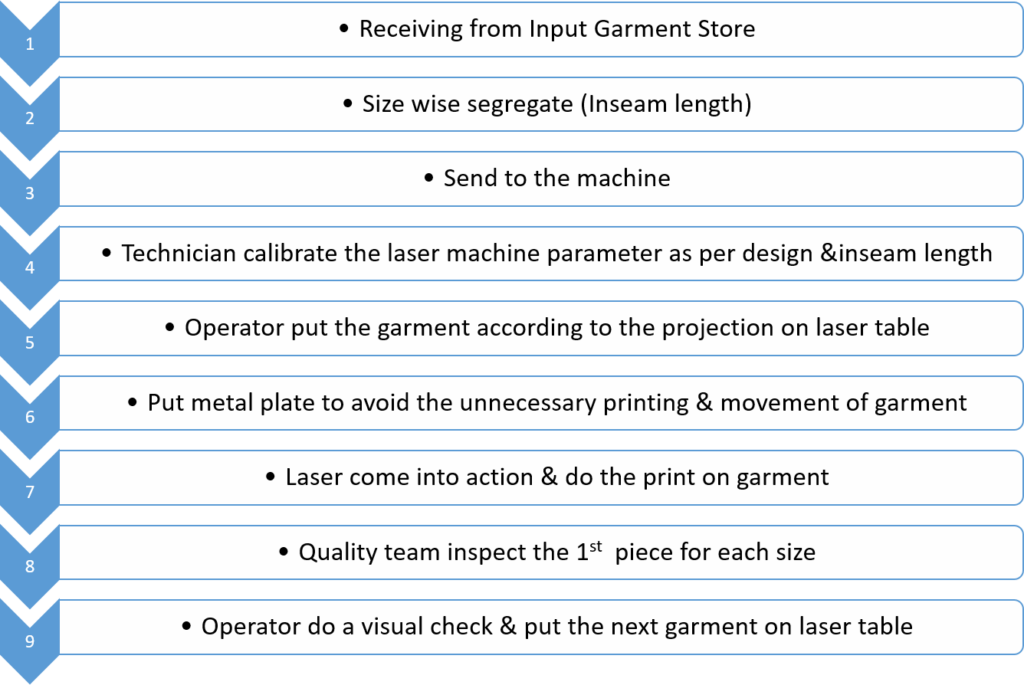
Initially hand sand & whisker is done manually. There is a chance of variation garment to garment. Once laser technology come into action the variation is reduce in significant level. A laser can complete this process in 90 seconds compared with up to 20 minutes in hand finishing.
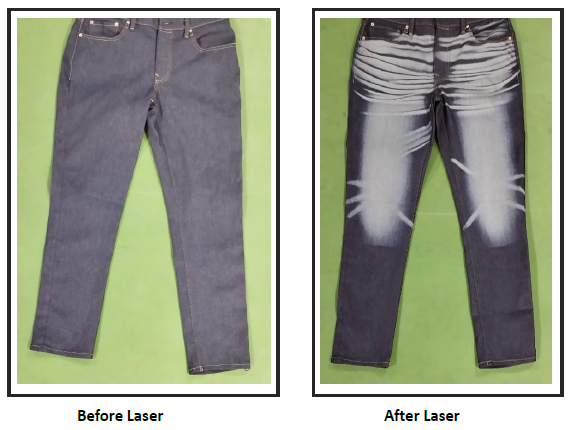
Machine Calibration Process:
There are three main machine parameters which decide the performance of the laser machine.
1. Laser Power:
This is the value which adjusts the laser power. It is expressed as a percentage. It is important to use the laser power at max level so that the machine can be used efficiently. Laser power doesn’t increase the laser burning speed but it will help to reduce time for other parameters which in turn increases efficiency.
2. Max Exposure time:
This is the indication of maximum waiting time of a laser beam on a point. With this parameter the burning power can be adjusted. When max Exposure time is increased the burning time also gets increased so burning will be slowed down & efficiency will get reduced. Once max exposure time is reduced the burning time will increase & efficiency will also get increased.
3. DPI:
Dot per inch, means number of dots available in an inch of area. DPI value is a parameter that affects the burning power. When DO I get increased the burning power also gets increased but the burning time gets slow. Burning at slow speed is a loss for production. So a standard DPI value should be chosen so that quality & quantity nothing is compromised.
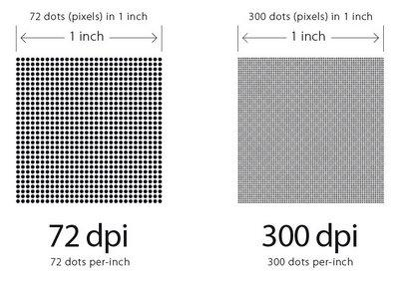
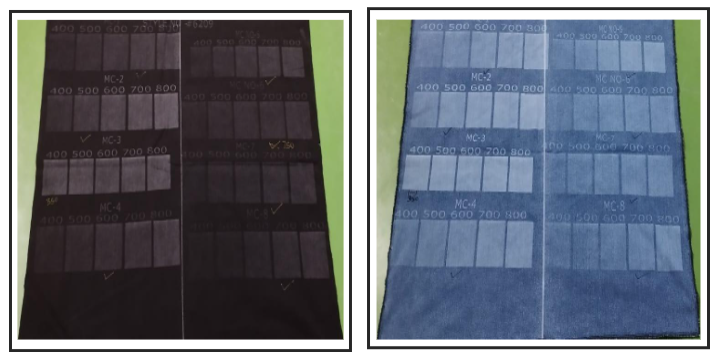
- Different fabric behavior is different in the same machine parameter.
- Even in the same fabric, same intensity but different machine shows different results.
- Need to confirm machine wise parameters for consistent result of garment.
Size wise segregation (Inseam length):
Inseam length wise garments need to separate before feeding in the machine.
As in many brands it has been found that in one waist band three different sizes of inseam has been found. So it is very important to separate the size.
The relation between inseam and waist band as below:
Inseam | Waist band Size |
28 | 26-28 |
30 | 29-30-31 |
30 | 32-33-34 |
30 | 36-38-40 |
32 | 29-30-31 |
32 | 32-33-34 |
32 | 36-38-40 |
34 | 29-30-31 |
34 | 32-33-34 |
34 | 36-38-40 |
36 | 32-33-34 |
Garment Feeding on Laser Table:
Feed in the laser machine is another critical work. There is a projector present in the laser machine. The projector makes an image in the feed plate. Garments need to be placed properly to get it printed. If the placement is wrong, then the garment will be rejected as the laser will print in the wrong place. Once a laser is printed there is no chance to make it correct.
Feeding position of the laser:
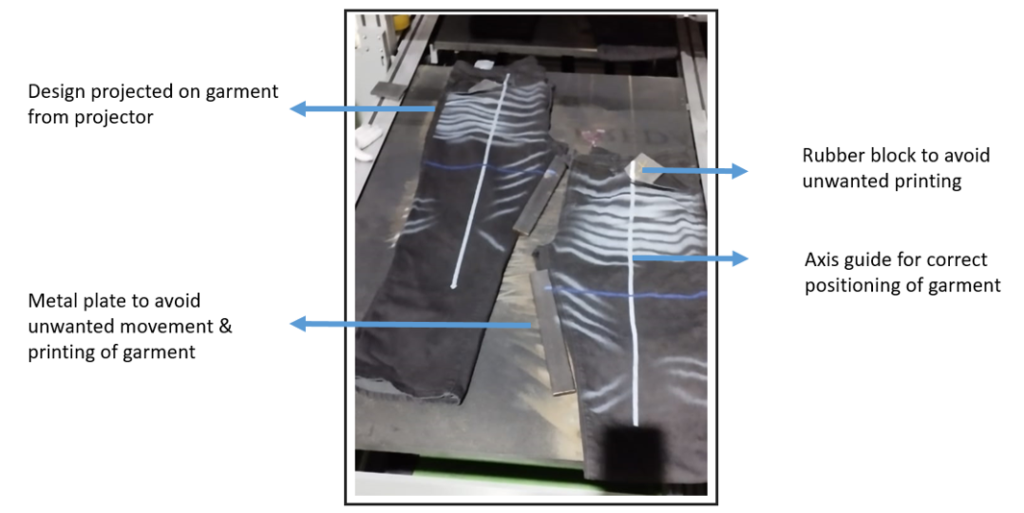
Conclusion:
Denim jeans are among the most popular articles of clothing on the planet. 4.5 billion pairs of them were sold in 2018 alone, meaning that at any given moment, approximately half of the entire global population are wearing these convenient, hard-wearing and stylish trousers. One study showed that To begin with, jeans consume a lot of resources. In order to grow sufficient cotton to create just one pair of denim trousers, 1,500 gallons of water are consumed. Yet not end, once we bring the pair of jeans & wash it at home the pollution is not stopped. Another research revealed that just one wash could be responsible for the release of 50,000 individual microfibers.
Laser wash is the best solution to avoid all this pollution & make the denim wash sustainable. Apart from that, the number of workers is reduced significantly & makes a wide range of designs with this laser. More we move toward sustainability, the more we need to grow interest in lasers to make the world a better place.
About the Author: Sourav Ghosh is a graduate of Govt. College of Engg. & Textile Technology, Serampore, West Bengal. Where he pursued his Bachelor's degree in textile Engineering. He worked with prestigious companies like Arvind Mills ( Ahmedabad) & Coats India ( Bangalore) in fabric development. He completed his Masters degree from the National Institute of Fashion Technology (New Delhi). Currently, he is working at Classic Fashion Apparel Ltd (Jordan) as an Operations Analyst.
- KVIC Young Professionals Recruitment 2025: Apply Online for Exciting Opportunities in Kolkata, Bhubaneswar, Patna & Ranchi
- Exploring the Future: Smart Textiles and Their Influence on Technological Innovation
- China’s Cotton Topping Robot: Revolutionizing Xinjiang’s Fields at 10x Speed
- Smart Garments for Elderly Health Monitoring and Active Living
- Redesigning the Breath of Life: A Next-Gen N95 That Filters More Than Air
онлайн с по выгодной цене
картина по фото на холсте картина по фото на холсте .
Изысканные холсты с печатью в студии, которые вдохнут на творчество.
Эксклюзивные холсты с печатью на заказ, которые украсят любой интерьер.
Творчество на холсте: лучшие мастера студии печати, для тех, кто ценит качество.
Индивидуальные холсты из студии печати, чтобы выделиться из толпы.
Студия печати: красочные идеи для подарков, для создания запоминающегося подарка.
картины на холсте картины на холсте .
Основные критерии выбора конкурсного управляющего, что важно знать, путь к успешной карьере, инсайдерская информация, Что нужно знать о конкурсном управлении: основные принципы, Эффективное управление в условиях конкурса, курсы для начинающих, Топ-советы по подбору конкурсного управляющего, проверенные стратегии, секреты профессии, эксклюзивные советы
конкурсный управляющий https://konkursnyj-upravlyayushhij.ru .
Выбор лучших магазинов мебели – только у нас
мебель италии купить https://kupit-mebel-italii.ru/ .
проект коттеджа https://tipovye-proekty-domov.ru .
что делает конкурсный управляющий http://konkursnyj-upravlyayushhij-po-bankrotstvu.ru/ .
купить мебель италия kupit-italyanskuyu-mebel.ru .
Secure Account Sales Account marketplace
Account exchange Guaranteed Accounts
account buying service find accounts for sale
account selling service accounts market
accounts market account marketplace
social media account marketplace https://accounts-marketplace.xyz/
buy account https://accounts-marketplace.live/
buy account https://accounts-marketplace.art
online account store https://accounts-marketplace.online/
buy account accounts marketplace
buy facebook ads manager buy-ads-account.click
buy old facebook account for ads ad-account-buy.top
buy facebook advertising https://buy-ads-account.work
buy facebook ad accounts buy fb ads account
buy bm facebook verified-business-manager-for-sale.org
buy tiktok business account https://tiktok-ads-account-buy.org
tiktok ads account buy https://tiktok-ads-account-for-sale.org
buy tiktok ads accounts buy tiktok ads
tiktok ads agency account https://tiktok-ads-agency-account.org