Introduction:
Cotton, one of the most widely used natural fibers, has a unique structure that imparts a variety of beneficial properties. Understanding these structural characteristics is essential for appreciating why cotton is so valued in the textile industry.
Cotton fiber, renowned for its natural comfort and versatility, owes much of its performance to its unique morphological structure. Comprising layers such as the cuticle, primary wall, secondary wall, and lumen, each part of the fiber contributes to the overall properties that make cotton a staple in the textile industry. These structural elements affect essential characteristics such as strength, flexibility, moisture absorption, and dyeability, making cotton an ideal choice for many applications in fashion and home textiles.
However, this post will focus on how the morphological structure of cotton fibers specifically impacts their properties and suitability for technical textiles and nonwovens. Despite the advantages, such as high absorbency and durability, cotton faces certain drawbacks when used in technical textiles and nonwoven fabrics. Challenges like its waxy surface, slurry formation in wet processes, and susceptibility to flammability can limit its performance in these sectors. This article will explore these limitations in depth while highlighting the critical role cotton fiber structure plays in shaping its overall properties.
Structure of Cotton Fiber:
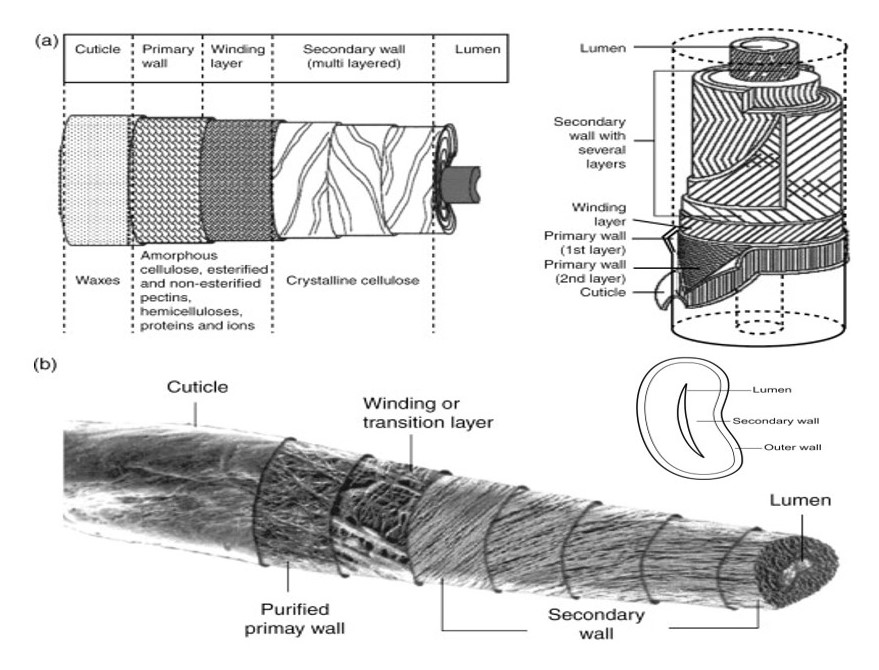
The image of the cotton fiber structure provides a detailed look at both the cross-section and longitudinal view of a cotton fiber. Here’s a simplified explanation:
Cross-Section View
- Cuticle: The outermost layer, which contains waxes and pectens, providing a protective coating.
- Primary Wall: Just beneath the cuticle, this layer is made of amorphous cellulose, hemicelluloses, and pectens.
- Secondary Wall: This is the thickest part of the fiber, consisting of multiple layers of crystalline cellulose, which gives the fiber its strength.
- Lumen: The central cavity of the fiber, which can collapse and twist, contributing to the fiber’s flexibility.
Longitudinal View
- Shows how these layers appear along the length of the fiber.
- The fiber twists, known as convolutions, which help in the spinning process and enhance the fiber’s flexibility and strength.
Properties of Cotton Fiber
1. Density and Moisture Regain
- Density: Cotton has a density of 1.52 g/cc, which contributes to its substantial feel and durability.
- Moisture Regain: Under standard conditions, cotton can regain up to 7% of its weight in moisture. This property is crucial for comfort, as it allows cotton to absorb sweat and keep the wearer dry.
2. Absorptive Capacity
- Cotton can absorb up to 24 times its own weight in water. This high absorptive capacity makes it ideal for towels, diapers, and other products where moisture absorption is key.
3. Fiber Structure
- Convolutions and Kidney Shape: The convoluted, kidney-shaped cross-section of cotton fibers enables them to make only random contact with the skin, enhancing comfort and breathability.
- Crystallinity: Cotton fibers are approximately 70% crystalline. This high degree of crystallinity contributes to their strength and durability.
4. Mechanical Properties
- Tenacity: Cotton’s tenacity ranges from 2.65 to 4.4 cN/dtex when dry and 2.9 to 5.7 cN/dtex when wet. This means cotton fibers are stronger when wet, which is beneficial for washing and wearing.
- Breaking Elongation: Cotton fibers have a breaking elongation of 3 to 9.5%, allowing them to stretch slightly without breaking.
- Elastic Recovery: Cotton can recover 74% of its original length after being stretched by 2%, which helps maintain the shape of cotton fabrics.
5. Chemical Resistance
- Cotton can withstand exposure to cold, weak acids but disintegrates when exposed to strong acids. This resistance to mild acids makes it suitable for various industrial applications.
- When exposed to sodium hydroxide (NaOH) concentrations of 18% or more, cotton fibers swell, which can be utilized in certain textile processing techniques.
6. Dyeing and Finishing
- Cotton can be dyed with a variety of dyes, including azoic, direct, reactive, sulfur, and vat dyes. This versatility in dyeing allows for a wide range of colors and patterns in cotton fabrics.
- Cotton can also be composted and sterilized, making it an environmentally friendly and hygienic option for many applications.
Drawbacks of Cotton in Nonwovens and Technical Textiles
Despite its many advantages, cotton has several drawbacks that limit its use in nonwovens and technical textiles:
- Waxy Surface: The natural waxy surface of cotton fibers makes bonding the carded web inefficient, if not difficult.
- Slurry Formation: In water for wet laying, cotton fibers form a slurry without additional dispersive chemicals, making the process impractical.
- Fine Particle Dust: Even the cleanest cotton fiber stock contains fine particle dust, which discourages its use in very hygienic applications where it would otherwise be well-suited.
- Short Fibers: Short fibers are either lost during web formation or create weak spots in the web due to uneven distribution.
- Flammability: Cotton burns and carries flame when exposed to fire, posing a risk in applications requiring flame retardancy.
Conclusion
The unique structural properties of cotton fibers make them an excellent choice for a wide range of textile applications. From their high moisture regain and absorptive capacity to their strength and dyeing versatility, cotton fibers offer a combination of comfort, durability, and functionality that is hard to match. However, the drawbacks of cotton, particularly in nonwovens and technical textiles, highlight the need for careful consideration of its use in specific applications. Understanding these properties helps in optimizing the use of cotton in various textile products, ensuring that it continues to be a staple in the industry.
Account Selling Platform Buy Account
Online Account Store Account Acquisition
find accounts for sale buy accounts
sell pre-made account buy and sell accounts
find accounts for sale https://accounts-offer.org
database of accounts for sale https://accounts-marketplace.xyz/
account buying platform https://accounts-marketplace.live
account trading https://accounts-marketplace.online
account store https://accounts-marketplace-best.pro
buy ad account facebook https://buy-ad-accounts.click
facebook accounts for sale facebook ad accounts for sale
buy facebook ads manager https://buy-ads-account.click
facebook ads account buy https://ad-account-buy.top
fb accounts for sale buy facebook profile
buy facebook account buy fb ad account
buy a facebook account https://ad-accounts-for-sale.work/
tiktok ads account buy https://tiktok-ads-account-buy.org
buy tiktok ads https://tiktok-ads-account-for-sale.org
tiktok ads agency account https://tiktok-agency-account-for-sale.org
tiktok ads agency account https://tiktok-ads-agency-account.org